
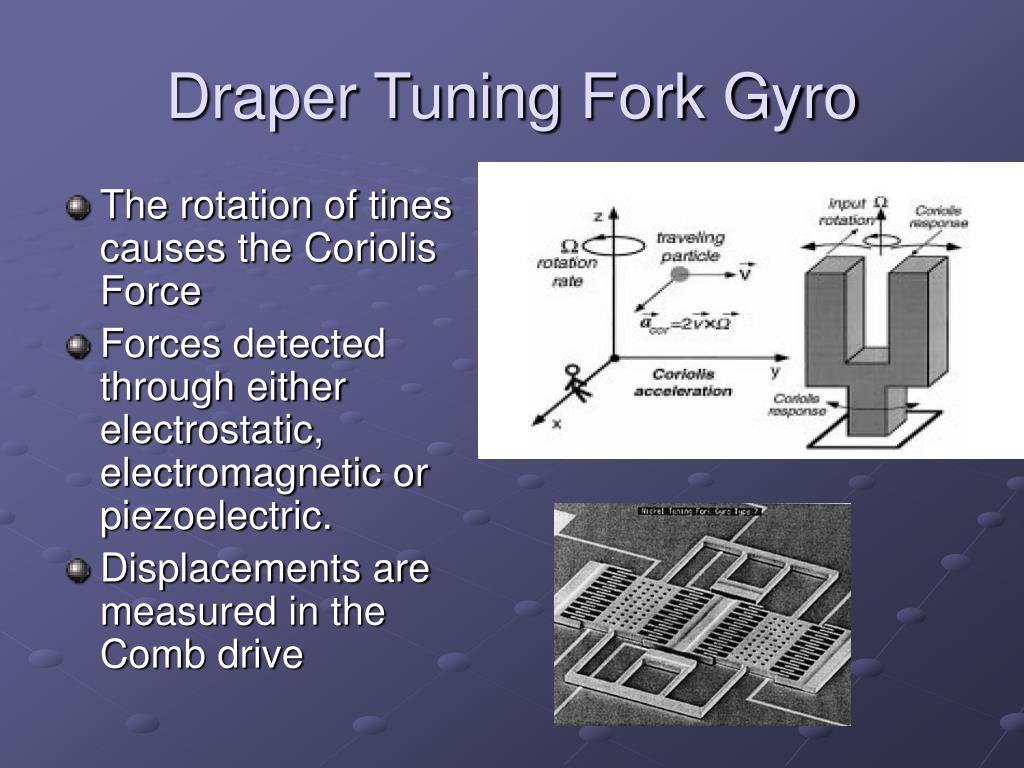
The angle between two adjacent antinode – nodes is 45 degrees. Standing waves are elliptically-shaped oscillations with four antinodes and four nodes located circumferentially along the rim. The Q-factor is usually about 20,000 that pre-determines its noise and angular random walks. The resonator is operated in its second-order resonant mode. This breakthrough technology gave a substantially increased product life (MTBF > 500,000 hours) with its shock resistance (>300G), it should qualify for "tactical" (mid-accuracy) applications. A recently patented variant by Innalabs uses a cylindrical design resonator made from Elinvar-type alloy with piezoceramic elements for excitation and pickoff at its bottom. in California, and piezo-ceramic variants by Watson Industries. Subsequently, in the 90s, CRGs with magneto-electric excitation and readout were produced by American-based Inertial Engineering, Inc. This type of gyroscope was developed by GEC Marconi and Ferranti in the 1980s using metal alloys with attached piezoelectric elements and a single-piece piezoceramic design. ( March 2011) ( Learn how and when to remove this template message)Ĭylindrical resonator gyroscope (CRG) Please help improve it by removing references to unreliable sources where they are used inappropriately. This section may contain excessive or inappropriate references to self-published sources. Inexpensive vibrating structure gyroscopes manufactured with MEMS technology are widely used in smartphones, gaming devices, cameras and many other applications.Ĭonsider two proof masses vibrating in plane (as in the MEMS gyro) at frequency ω r. Vibrating structure gyroscopes are simpler and cheaper than conventional rotating gyroscopes of similar accuracy. The Coriolis effect causes the object to exert a force on its support, and by measuring this force the rate of rotation can be determined. The underlying physical principle is that a vibrating object tends to continue vibrating in the same plane even if its support rotates. A vibrating structure gyroscope functions much like the halteres of flies ( insects in the order Diptera). The experimental results show that the output speed of the actuator is positively linearly related to the excitation voltage, the maximum output thrust is 8 N when the excitation voltage is 100 V, the excitation frequency is 20.1 kHz, the pre-pressure is 7.5 N, the phase difference of the excitation signal is π/2, and the output speed of the actuator can reach 116 mm/s.A vibrating structure gyroscope, defined by the IEEE as a Coriolis vibratory gyroscope ( CVG), is a gyroscope that uses a vibrating structure to determine the rate of rotation. After optimizing the stator chamfer to 2.5 and 4.5 mm, the tangential amplitude difference of the 15° tuning fork angle actuator is the smallest. The simulation results show that the integrated output performance of the piezoelectric actuator is best when the angle of the tuning fork is 15°. The externally applied conditions (the influence model of excitation voltage, excitation frequency, and pre-pressure) on the performance output of piezoelectric actuators will promote the miniaturization and industrialization of tuning fork piezoelectric actuators in the next step. Aiming at the problems of low output speed, large size, and difficult miniaturization of stacked and sandwich piezoelectric actuators, a patch-type tuning fork piezoelectric actuator model based on the stick-slip effect was designed, in which the dynamic theoretical analysis, the simulation optimization to determine the stator structure parameters, and the experimental research were carried out to obtain the stator structure parameters.
